BISO 3D VARIOFLEX•AIR•i
Premium header in new 3D class
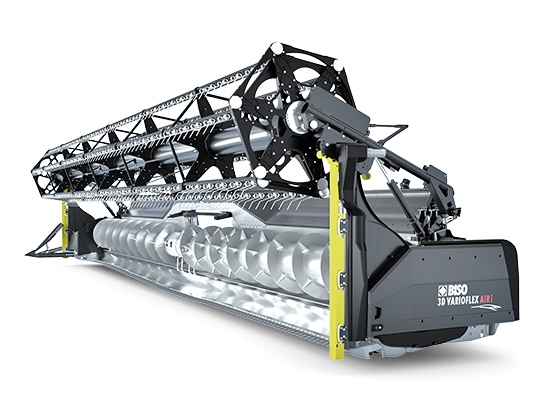
An efficient and relaxed harvest begins with the premium header. Premiums will include models that can harvest not only cereals, rape or soybeans, but also laid wheat or barley in the FLEX mode, even in shots over 9m. And all this with a precise cut at the required height in every situation.
The VARIO and the intake auger remain the basis of the header
From the point of view of combine harvesters, Europe is generally wetter than the rest of the world, or at least than North America, Australia or the specific Kazakhstan. That is why we follow a slightly different direction in Europe. The intake auger has a dominant position here not only due to its performance and quality of work, but above all its durability and low operating costs. When buying a modern combine harvester in Europe, our customers already take the VARIO type header as a matter of course. As a kind of standard. However, the structure of crops, the growing organizational stress resulting from changes in the weather and the varietal composition and the demands of farmers are constantly pushing the requirements for this technology forward. The performance of the combine harvesters has increased significantly over the last 20 years, and it must be admitted that in operation, the combine harvester is often limited by the header. Due to high yields and climate change, "lagers" are often harvested, where money literally lies on the ground. And so we get to the logical requirement for the FLEX module.
The award-winning BISO VARIOFLEX AIR i header and the new 3D class, equipped with the BISO VARIO and FLEX systems in combination with the AIR air suspension and the intelligent "i" control system.
FLEX module parallelogram
The 3D header is a new dimension. To be in this new class, you must have the cutter bar hung in such a way that when you copy in FLEX mode, the inclination of the cutter bar and the double fingers and the resulting cutting angle do not change. And this is ensured with our rails by using a parallelogram in combination with air suspension and an intelligent movement control system for each hinge. And it is done completely separately from the others. Thanks to the patented pressure sensing on the ground, we are able to set the pressure from 0-50 kg. For comparison, it should be noted that the classic mechanical flex module, for example on our CropRanger VX TLL FLEX header, needs a force corresponding to about 50 kg for lightening at one point. The competition is usually around 80 kg. BISO has been cooperating with important/key manufacturers for many years and their placing/order for the header of the future sounded clear - 5 kg. And you simply can't reach this parameter with classic mechanics.
Fully automatic mode
Everyone who rides a combine harvester will certainly confirm that a standard 7.5 m header cannot be supervised. That is why the professional combine crews have a liking for a number of clever assistants that monitor as many functions as possible automatically and, above all, are able to react in a flash. For headers of large shots (now commonly 9m, 10.7m or 12m) we are primarily dependent on a perfectly functioning thresher copier. These systems are now at a very high level and are the basis for the correct functions of the FLEX module. Typical of BISO headers is the so-called tip tilt, where the driver can tilt the cutter towards or away from him while driving and thus, in combination with the extension of the VARIO cutting deck, acquires a number of harvesting strategies. For BISO VARIOFLEX AIR i headers with intelligent control of the FLEX module, the header always moves in automatic mode when the FLEX mode is activated by the combine driver. The driver only lowers the header to the working position and sets the required ground pressure according to the harvesting conditions and the type of soil. If the active work of the FLEX module is not required, he deactivates it and the system retracts automatically. Then, the header works as standard with a fixed table with the VARIO system.
Reel cutter bar collision control
For a fully automatic travel of the header in the FLEX mode, it is necessary to solve the risk of contact of the reel tines of the reel drive with the cutting knife at the moment when the FLEX module is raised at a certain place. And this commonly happens when copying the terrain. There are a number of solutions on the market, especially American ones, where a compromise is made. The reel tines of the reel drive are plastic and if there is a situation where the driver does not watch over the reel drive and the reel tines hit the cutting knife, they are simply shortened and then they must be replaced. In Europe, however, the requirements for the feeder are relatively high when harvesting lying crops or BIO soybeans, so we use flexible spring steel reel tines, which can lift even heavy vegetation at the right moment above the cutter knife. For this reason, the "AIR i" mower decks are equipped with an intelligent system that monitors each hinge of the FLEX system, and when there is a risk of a collision between the FLEX module and the flexible reel tines of the reel drive, it is lifted immediately and completely automatically.
A hybrid frame for a longer lifespan
The basis of the long lifespan of the header is a solid frame and a high-quality transport trailer. You will not recognize a quality header after a year of operation, but after 10,000 ha and thousands of kilometers travelled on a trailer. The steel header works well up to a maximum of 9 m. Already in this engagement, the steel frame springs so much that the service life of all the bearings of the intake auger and other drives suffers significantly.
For hybrid frames that combine aluminium with steel, the suspension is minimal and their benefits will be appreciated by the customer only after several years of operation. The full benefits of this technology are already evident in the 12-meter headers. For the first time, we used this technology on the 3rd generation Ultralight headers, where customers appreciated its real benefits only after several years of operation. The extremely strong hybrid frame is also a basic prerequisite for a well-functioning VARIO with an extension of 800 mm and the ability to slide the cutter knife almost under the intake auger. In practice, this means that we can pull to an intake auger at a distance of only 170 mm. And this is the value that interests you when harvesting extremely short barley.
Harvesting regimes and strategies
The BISO 3D VARIOFLEX AIR i header offers the owner a whole range of strategies for harvesting various crops. In the rape, extend the VARIO almost to the maximum, place the dividers on the cart and switch on the hydraulic side knives. In wheat, most crews use a strategy of extending the VARIO in such a way that the stalks go under the intake auger and thus into the thresher by "ear ahead" in order to achieve easier threshing and a smoother flow of material. But there can also be situations where you harvest entwined vegetation and place side mowers behind the mounted dividers and activate them. A similar situation can occur in weedy soybeans, when you also activate the FLEX module and extend the VARIO according to specific conditions. Every growth is different. In the same way, in lagers, you activate the FLEX module as in soybeans or peas, you usually put the bar slightly on top and extend the VARIO so that you have an overview of the material that goes into the thresher. And if possible, everything went as smoothly as it could. If you are on a rocky plot, you will probably extend the VARIO almost to the max just so that you have enough time to see and hear the stone and stop inserting. This is a general advantage of the VARIO system, which is not much talked about. But it can save you a lot of money on critical plots. In such a situation, it is very important to "hit" the correct angle of the entire header, the mentioned "tilting to the tip". BISO headers have not had competition in lagers for a long time, but it should be mentioned that the use of jacks is a matter of a few minutes and by using them you save the cutting knife in particular.
One header for all crops
> no additional header or attachments for special crops needed
> harvesting different crops without time consuming adjustments of the header
> no additional maintenance due to its simple, reliable floor structure – keeping the proven variosystem
> no losses due to its intelligent ground-following system – Flexmode
> the smallest distance for the auger – cutter knife – is only 180 mm, excellent for short crop harvesting
> with the correct application, the ears of the grain come first to the threshing drum – excellent performance of the combine
> practical application for all known crops
> stress-free harvesting – clear relief of stress on the driver
Available equipment levels
The best-equipped model is the VARIOFLEX AIR i, which has air suspension and an intelligent control system with a tablet in the cabin with the possibility of setting the pressure from 0 - 50 kg and many other automatic functions. There is currently no alternative to this model on the market. A more available variant will be VARIOFLEX AIR "without a small" i ", which will have air suspension, but without the mentioned" intelligence ", i.e. without sensing the force on the FLEX module. It will be our reaction to some competing products with air or hydraulic suspension and with the FLEX module. And for customers who do not need the FLEX module, there will be a standard 2D VARIO model in offer, which will have a modern hybrid frame and the proven and patented BISO VARIO system, but without the FLEX module. The 9.2m model is very interesting, because it has the drives from both sides and therefore the load on the cutting knife and on the drives is minimal even in extremely demanding conditions.
We wish all customers loyal to BISO technology a successful season and thank you for your cooperation.
Other interesting articles: