BISO 2D – PERFECT IN DETAIL
BISO 2D VARIO 770 - 1560 COMBINE HEADER RANGE
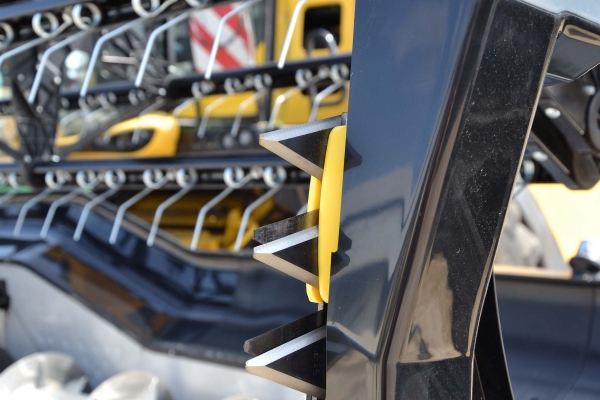
The BISO 2D VARIO series of combine headers covers working widths from 7.7 m to 15.6 m. This would not have been possible without the hybrid frame and other key technologies that make this range the market leader in headers with auger. In this article, let's take a look at some interesting details that will give a better idea of the level of workmanship and technology used on this series.
BISO 2D920 VARIO header.
The lower part of the header is completely covered and we only supply the hardox variant for this premium series.
In this picture you can clearly see the set of parts for connection to the feeder house of the combine, which can be additionally exchanged according to the brand. The design of the hybrid frame (riveted joints between steel parts and the aluminium support profile) is also clearly visible.
When a new header is delivered, the so-called wings are installed, i.e. the extension of the screw to the centre of the feeder house. These extensions are used only in dry years with a very small volume of mass. Therefore, they are usually dismantled on machines in operation.
In the same way, one segment of the wiper blade is dismantled in relation to the extended wings.
Connecting the header to the combine harvester, the so-called scooping up of the header. All connection points, including the mechanical locking of the feeder house, are on the left side of the driver's position. On the right side of the 2D920 model, only the second cardan shaft needs to be attached (and possibly unlock the copier skids).
The connection procedure is the same as we are used to with other headers.
The moment of "scooping up" the black beam of the header. This beam slides in a special bearing and by moving it against the bar frame, we change the so-called tilt to the tip, i.e. the angle of the header. The picture shows the connection to the New Holland CR combine, hence the typical quick-release hydraulic block and two sockets – the upper standard New Holland and the lower one for BISO control.
View of the attachment points of the cutter bar for CNH combine's harvesters.
BISO 2D VARIO is a header with a high-performance auger. The picture clearly shows the robustness of the auger and the console of its central support. In this picture, the VARIO is retracted.
And now the VARIO pulled out. You can see that the sides of the header are also moving, so are the dividers and, of course, the side knifes.
This is what the 70cm VARIO pull-out looks like in practice. For operational reasons, we stick to a tried-and-tested concept for side drives. That is, the main drive belt of the knife and the drive chain for the auger located behind it. The drives of the 2D920 are ambidextrous.
The side walls on this model series are steel, welded. Not aluminium castings. We returned to this option because of easier repairs in operation, because the sidewalls are often exposed to minor damage, especially on large headers.
Knife drive gearbox – a typical solution for BISO. Traditionally, we use the so-called high-speed knife without overrun, as is currently common.
This picture shows the so-called transition knife head for the Schumacher system (knife and double-fingers). There should be a spare knife lever, a bolt and a knife head with accessories in the harvester. We lubricate the grease nipple on the knife head during morning maintenance.
Double-fingers and Schumacher knife. A solution that is mainly used by owners of JD, Laverda and Deutz-Fahr machines. We order this variant for stony soil, for harvesting of peas or soybeans.
In the picture, in the lower part, under the double fingers, at a certain distance from each other, rollers with shoulders for quick clamping of crop lifters are visible. It will take a few minutes to put the jacks on this bar. This is the standard BISO solution we are used to.
Close-up of the crop lifters attachment system. Also evident is the typical design for Schumacher knife, where the segments of the knife are alternately turned and the double-fingers have upper and lower blades.
The central section, i.e. the place where the two knifes meet and slide over each other. It is necessary to have several segments of the knife with countersunk screws.
Behind the knife there is a distinct "hump". Like the entire bottom, it is made of stainless steel. It is used to capture stones and is always a compromise between the ability to capture stone and limit the flow of matter. It works very well in operation, and many stones remain "sitting in the space between the knife and this hump.
Central bracket of the auger. Thanks to this solution and drives from both sides, the load is halved.
The actual design of the center console.
There are two small wings on the auger that spread the material around the central console.
Classic BISO auger finger design with openable yellow sleeve inside. There is no need to dismantle the shaft for replacement.
Tensioning of the drive chain of the auger on its chain idler pulley. Adjustment and control - easy according to the red gauge.
The chains are carefully routed on plastic gliders with automatic lubrication.
Adjustable bracket rollers on which the VARIO table slides out.
Checking the knife drive belt tension.
Knife drive gearbox pulley.
We use a standard proven knife drive. Gearbox with oil filling, knife lever, shear locking bolt of the knife head and the knife head itself with a grease nipple.
In the upper left and right corners of the feeder house there are hydraulic cylinders "tilting to the tip".
Hydraulic cylinders "tilting to the tip" in detail.
The reel combines steel, aluminium and plastic parts. Interestingly, thanks to the special pre-tensioning, we use a one-piece reel up to a working width of 12.3m.
The hydraulic motor of the reel drive is on the right side and is integrated into its central tube.
The flexible tines of the spring steel reel are secured in an aluminium tube by a single screw, which at the same time serves as a protection against winding long stalks.
In this picture, the kinematics of the reel are clearly visible. Under the black cover is an electric motor to adjust the angle of inclination of the reel fingers. At the bottom, there are rollers that prevent the fingers from coming into contact with the knife.
A dark red latch can be seen on the hydraulic cylinder for lifting the reel, which allows you to leave the reel in a slightly raised position before disconnecting the header and placing it on the trolley for easier morning maintenance.
Side knifes in the standing position for rapeseed harvesting.
Double mounting of side knifes. A solution typical of BISO for many years.
On the 2D model series, we use only side knifes with a hydraulic drive.
Wedo not use any skid in the lower part of the side knife because of maximum aggressiveness in heavily weeded vegetation and the ability to work almost at the ground.
The drive of the hydraulic pump for the side knifes drive is from the main countershaft drive shaft and is traditionally solved by a chain.
View of the hydraulics layout. It is obvious at first glance that it is based on the hydraulic concept of the CropRanger model series.
Control block with solenoids.
Hydraulic oil tank and water tank for hand washing. Both integrated into the grain splash guard.
Tool box.
The individual components of the hydraulic system are very easily accessible and logically placed on this rail.
There are 4 copier skids used, the outer ones are larger and the inner ones are smaller.
A simple system for securing the skids in a raised position for transport on a trailer.
View of the stainless-steel bottom of the VARIO table and the design of the sidewall when extended. It is evident from the design that when the VARIO table is extended, the copier skids also move forward with the cutter bar.
According to thebrand of the combine, the header is fitted with potentiometers of the given brand. Their calibration is therefore carried out as part of the standard calibration of the combine.
The picture shows a simpler design of the divider. Popular especially for its low weight and very compact design. Fully adjustable dividers are also produced.
More about the 2D VARIO cutter bars:
https://navigator.biso.eu/en/en-biso/harvesting-technics/biso-3d-varioflex-air-i/
Brochure in CZ version for download:
https://navigator.biso.eu/wp-content/uploads/2020/04/BISO-3D-VARIOFLEX-AIR-i-ENG.pdf
Other interesting articles: